8.2 The Reaction of Biodiesel: Transesterification
So, how do we make biodiesel?
The method being described here is for making FAMEs biodiesel. The reaction is called transesterification, and the process takes place in four steps. The first step is to mix the alcohol for reaction with the catalyst, typically a strong base such as NaOH or KOH. The alcohol/catalyst is then reacted with the fatty acid so that the transesterification reaction takes place. The first figure below shows the preparation of the catalyst with the alcohol, and the second figure shows the transesterification reaction.

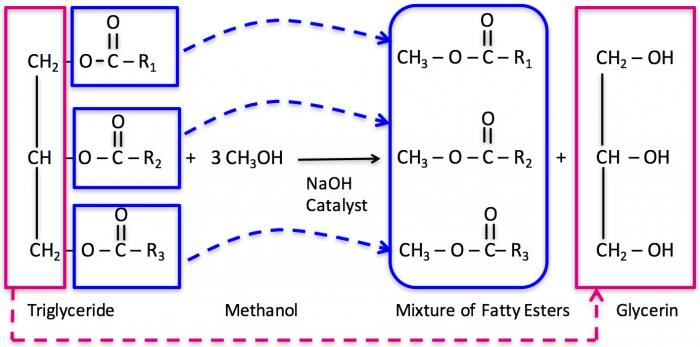
The catalyst is prepared by mixing methanol and a strong base such as sodium hydroxide or potassium hydroxide. During the preparation, the NaOH breaks into ions of Na+ and OH-. The OH- abstracts the hydrogen from methanol to form water and leaves the CH3O- available for reaction. Methanol should be as dry as possible. When the OH- ion reacts with H+ ion, it reacts to form water. Water will increase the possibility of a side reaction with free fatty acids (fatty acids that are not triglycerides) to form soap, an unwanted reaction. Enzymatic processes can also be used (called lipases); alcohol is still needed and only replaces the catalyst. Lipases are slower than chemical catalysts, are high in cost, and produce low yields.
Once the catalyst is prepared, the triglyceride will react with 3 mols of methanol, so excess methanol has to be used in the reaction to ensure a complete reaction. The three attached carbons with hydrogen react with OH- ions and form glycerin, while the CH3 group reacts with the free fatty acid to form the fatty acid methyl ester.
The figure below is a graphic of the necessary amounts of chemicals needed to make the reaction happen and the overall yield of biodiesel and glycerin. The amount of methanol added is almost double the required amount so the reaction goes to completion. With 100 lbs of fat and 16-20 lbs of alcohol (and 1 lb of catalyst), the reaction will produce 100 lbs of biodiesel and 10 lbs of glycerin. The reaction typically takes place at between 40-65°C. As the reaction temperature goes higher, the rate of reaction will increase, typically 1-2 hours at 60 °C versus 2-4 hours at 40°C. If the reaction is higher than 65°C, a pressure vessel is required because methanol will boil at 65°C. It also helps to increase the methanol-to-oil ratio. Doubling the ratio of 3 mols of alcohol to 6 mols will push the reaction to completion faster and more completely.

The following video shows a time-lapsed reaction of transesterification of vegetable oil into biodiesel. It also incorporates the steps after the reaction to separate out the biodiesel (9:44).
The figure below shows a schematic of the process for making biodiesel. Glycerol is formed and has to be separated from the biodiesel. Both glycerol and biodiesel need to have alcohol removed and recycled in the process. Water is added to both the biodiesel and glycerol to remove unwanted side products, particularly glycerol, that may remain in the biodiesel. The wash water is separated out similar to solvent extraction (it contains some glycerol), and the trace water is evaporated out of the biodiesel. Acid is added to the glycerol in order to provide neutralized glycerol.

As briefly discussed, the initial reactants used in the process should be as dry as possible. Water can react with the triglyceride to make free fatty acids and a diglyceride. It can also dissociate the sodium or potassium from the hydroxide, and the ions Na+ and K+ can react with the free fatty acid to form soap. The figure below shows how water can help to form a free fatty acid, and that free fatty acid can react with the Na+ ion to form soap. The sodium that was being used for a catalyst is now bound with the fatty acid and unusable. It also complicates separation and recovery. All oils may naturally contain free fatty acids. The refined vegetable oil contains less than 1%, while crude vegetable oil has 3%, waste oil has 5%, and animal fat has 20%. Animal fats are a less desirable feedstock.
