2.2 Refining of Petroleum into Fuels
Much of the content in this particular section is based on information from Harold H. Schobert, Energy and Society: An Introduction, 2002, Taylor & Francis: New York, Chapters 19-24.
The following is a simplified flow diagram of a refinery. Since it looks relatively complicated, the diagram will be broken into pieces for better understanding.
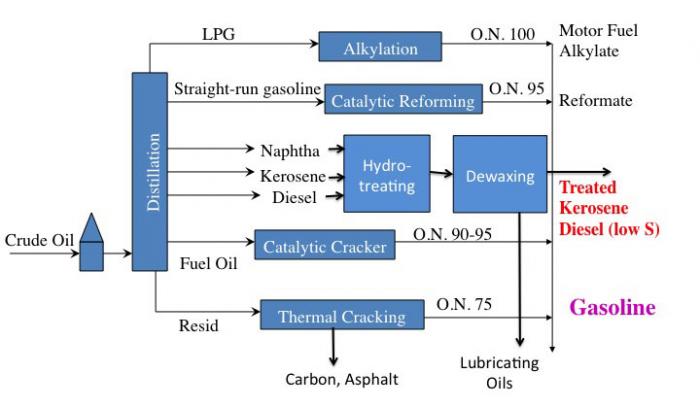
Crude oil enters and goes to distillation. From distillation:
- LPG (gases) goes through alkylation to become O.N. 100 Motor Fuel Alkylate which can go on to become gasoline.
- Straight-run gasoline goes through catalytic reforming to become O.N. 95 Reformate which can go on to become gasoline.
- Naphtha, Kerosene, and Diesel all go through Hydrotreating and then dewaxing to become either treated Kerosene, Diesel (low sulfur), or lubricating oils.
- Fuel Oil goes through a catalytic cracker to become O/N 90-95 Gasoline.
- Resid goes through Thermal Cracking to become either Carbon, Asphalt, or O.N. 75 Gasoline.
Distillation
We will start with the first step in all refineries: distillation. Essentially, distillation is a process that heats crude oil and separates it into fractions. It is the most important process of a refinery. Crude oil is heated, vaporized, fed into a column that has plates in it, and the materials are separated based on the boiling point. It indicates that as the liquids are separated, the top-end materials are gases and lighter liquids, but as you go down the column, the products have a higher boiling point, the molecular size gets bigger, the flow of the materials gets thicker (i.e., increasing viscosity), and the sulfur (S) content typically stays with the heavier materials. Notice we are not using the chemical names, but the common mixture of chemicals. Gasoline represents the carbon range of ~ C5-C8, naphtha/kerosene (aka jet fuel) C8-C12, diesel C10-C15, etc. As we discuss the refinery, we will also discuss the important properties of each fuel.
The most important product in the refinery is gasoline. Consumer demand requires that 45-50 barrels per 100 barrels of crude oil processed are gasoline. The issues for consumers are, then: 1) quality suitability of gasoline and 2) quantity suitability. The engine that was developed to use gasoline is known as the Otto engine. It contains a four-stroke piston (and engines typically have 4-8 pistons). The first stroke is the intake stroke - a valve opens, allows a certain amount of gasoline and air, and the piston moves down. The second stroke is the compression stroke - the piston moves up and valves close so that the gasoline and air that came in the piston during the first stroke are compressed. The third stroke happens because the spark plug ignites the gasoline/air mixture, pushing the piston down. The fourth stroke is the exhaust stroke, where the exhaust valve opens and the piston moves back up. There is a good animation in How Stuff Works (Brain, Marshall. 'How Car Engines Work' 05 April 2000. HowStuffWorks.com).

The products that come out of distillation are gases, gasoline, naphtha, kerosene, diesel, heating oils, and resid. In that order boiling point increases, molecular size increases, viscosity increases, and usually the sulfur content increase.

Four strokes of Otto gasoline engine
- Intake stroke. The piston moves down. The intake valve opens.
- Compression stroke. The piston moves up. The valves close.
- Power stroke. The piston moves down. The valves closed.
- Exhaust stroke. The piston moves up. The exhaust valve opens.
You'll notice the x and the y on strokes 1 and 2. The ratio of x/y is known as the compression ratio (CR). This is a key design feature of an automobile engine. Typically, the higher the CR, the more powerful the engine is and the higher the top speed. The "action" is in the ignition or power stroke. The pressure in the cylinder is determined by 1) pressure at the moment of ignition (determined by CR) and 2) a further increase in pressure at the instant of ignition. At higher pressures with the CR, the more likely the pressure will cause autoignition (or spontaneous ignition), which can cause "knocking" in the engine - the higher the CR, the more likely the engine will knock. This is where fuel quality comes in.
For gasoline engines, the CR can be adjusted to the fuel rating to prevent knocking; this fuel quality is known as the "octane" number. Remember the straight-chain alkanes in the chemistry tutorial? The straight-chain alkanes are prone to knocking. The branched alkanes are not. The octane number is defined as 1) heptane - octane number equal to 0, and 2) 2,2,4-trimethylpentane - octane number equal to 100 (this is also known as "octane"). See the figure below for the chemical structures of heptane and octane for octane numbers. Modern car engines require an 87, 89, or 93-94 octane number. However, when processing crude oil, even high-quality crude oil, we can only produce from a distillation yield of 20% with an octane number of 50. This is why crude oil needs to be processed, to produce gasoline at 50% yield with an octane number of 87-94.

Other ways to improve the octane number:
- Add aromatics. Aromatics have an octane number (ON) greater than 100. They can be deliberately blended into gasoline to improve ON. However, many aromatic compounds are suspected carcinogens, so there are regulatory limits on the aromatic content in gasoline.
- Another approach to increasing ON is to add alcohol groups. Methanol and ethanol are typical alcohols that can be added to fuel. ON is ~110. They can be used as blends with racing cars (known as "alky").
But even with these compounds, distillation will not produce enough gasoline with a high enough ON. So other processes are needed.
"Cracking" Processes
Thermal cracking
One way to improve gasoline yield is to break the bigger molecules into smaller molecules - molecules that boil in the gasoline range. One way to do this is with "thermal cracking." Carbon Petroleum Dubbs was one of the inventors of a successful thermal cracking process. The process produces more gasoline, but the ON was still only ~70-73, so the quality was not adequate.
Catalytic cracking
Eugene Houdry developed another process; in the late 1930s, he discovered that thermal cracking performed in the presence of clay minerals would increase the reaction rate (i.e., make it faster) and produce molecules that had a higher ON, ~100. The clay does not become part of the gasoline - it just provides an active surface for cracking and changing the shape of molecules. The clay is known as a "catalyst," which is a substance that changes the course of a chemical reaction without being consumed. This process is called "catalytic cracking". The figure below shows the reactants and products for reducing the hexadecane molecule using both reactions. Catalytic cracking is the second most important process of a refinery, next to distillation. This process enables the production of ~45% gasoline with higher ON.

Below is the refining schematic with the additional processing added.

There are also tradeoffs when refineries make decisions as to the amount of each product they make. The quality of gasoline changes from summer to winter, as well as with gasoline demand. Prices that affect the quality of gasoline include 1) the price of crude oil, 2) the supply/demand of gasoline, 3) local, state, and federal taxes, and 4) the distribution of fuel (i.e., the cost of transporting fuel to various locations). Below is a schematic of how these contribute to the cost of gasoline and diesel.

Additional Processes
Alkylation
The alkylation process takes the small molecules produced during distillation and cracking and adds them to medium-sized molecules. They are typically added in a branched way in order to boost ON. An example of adding methane and ethane to butane is shown below.

Catalytic Reforming
A molecule may be of the correct number of carbon atoms but need a configuration that will either boost ON or make another product. The example below shows how reforming n-octane can produce 3,4-dimethyl hexane.

So, let's add these two new processes to our schematic in order to see how they fit into the refinery, and how this can change the ON of gasoline. The figure below shows the additions, as well as adding in the middle distillate fraction names. Typically, naphtha and kerosene, which can also be sold as these products, are the products that make up jet fuels. So, our next topic will cover how jet engines are different from gasoline engines and use different fuel.

This is a simple flow diagram of a crude oil refinery.
Crude oil enters and goes to distillation. From distillation:
LPG (gases) goes through alkylation to become O.N. 100 Motor Fuel Alkylate which can go on to become gasoline
Straight-run gasoline goes through catalytic reforming to become O.N. 95 Reformate which can go on to become gasoline
Naphtha, Kerosene, and Diesel become jet fuels.
Fuel Oil goes through a catalytic cracker to become O.N 90-95 Gasoline
Resid goes through Thermal Cracking to O.N. 75 Gasoline.