
The process of crude oil refining
Despite all of the attention that it gets, no one actually wants crude oil – what people want are the various products that are derived from crude oil. These products include not only gasoline, heating oil, and so forth (which will be the focus of our discussions) but everyday consumer items like plastics, long underwear, and crayons. In this lesson, we’ll discuss markets for energy commodities that are refined from petroleum. While conditions in the crude oil market are highly influential in determining the prices of these products, in some sense each petroleum product market has a life of its own.
Once crude oil is extracted from the ground, it must be transported and refined into petroleum products that have any value. Those products must then be transported to end-use consumers or retailers (like gasoline stations or the company that delivers heating oil to your house, if you have an oil furnace). The overall well-to-consumer supply chain for petroleum products is often described as being segmented into three components (shown graphically in Figure 10.6).
- Upstream activities involve exploring for crude oil deposits and the production of crude oil. Examples of firms that would belong in the upstream segment of the industry include companies that own rights to drill for oil (e.g., ExxonMobil) and companies that provide support services to the drilling segment of the industry (e.g. Halliburton).
- Midstream activities involve the distribution of crude oil to refiners; the refining of crude oil into saleable products; and the distribution of products to wholesalers and retailers. Examples of firms that would belong in the midstream segment of the industry include companies that transport oil by pipeline, truck or barge (e.g., Magellan Pipeline); and companies that refine crude oil (e.g., Tesoro).
- Downstream activities involve the retail sale of petroleum products. Gasoline stations are perhaps the most visible downstream companies, but companies that deliver heating oil or propane would also fall into this category.

Some companies in the petroleum industry have activities that would fall into upstream, midstream and downstream segments. ExxonMobil is one example of such a firm. Others have activities that fall primarily into only one segment. The KinderMorgan pipeline company is an example of a specialized petroleum firm, in this case belonging to the midstream segment. Many regions have local gas station brands that would specialize in the downstream segment of the industry. One of the best-known regional examples is the WaWa chain of gas stations and convenience stores in eastern Pennsylvania, but large grocery stores and retailers like Costco and Wal-Mart are increasingly involved in downstream sales of petroleum products.
Petroleum refineries are large-scale industrial complexes that produce saleable petroleum products from crude oil (and sometimes other feedstocks like biomass). The details of refinery operations differ from location to location, but virtually all refineries share two basic processes for separating crude oil into the various product components. Actual refinery operations are very complicated, but the basic functions of the refinery can be broken down into three categories of chemical processes:
- Distillation involves the separation of materials based on differences in their volatility. This is the first and most basic step in the refining process, and is the precursor to cracking and reforming.
- Cracking involves breaking up heavy molecules into lighter (and more valuable) hydrocarbons.
- Reforming involves changing the chemical nature of hydrocarbons to achieve desired physical properties (and also to increase the market value of those chemicals).
The link below will take you to a 10-minute video that provides more details on the various refining processes.
Video: Petroleum Refining Basics (10:00)
The first process is known as distillation. In this process, crude oil is heated and fed into a distillation column. A schematic of the distillation column is shown in Figure 10.7. As the temperature of the crude oil in the distillation column rises, the crude oil separates itself into different components, called “fractions.” The fractions are then captured separately. Each fraction corresponds to a different type of petroleum product, depending on the temperature at which that fraction boils off the crude oil mixture.

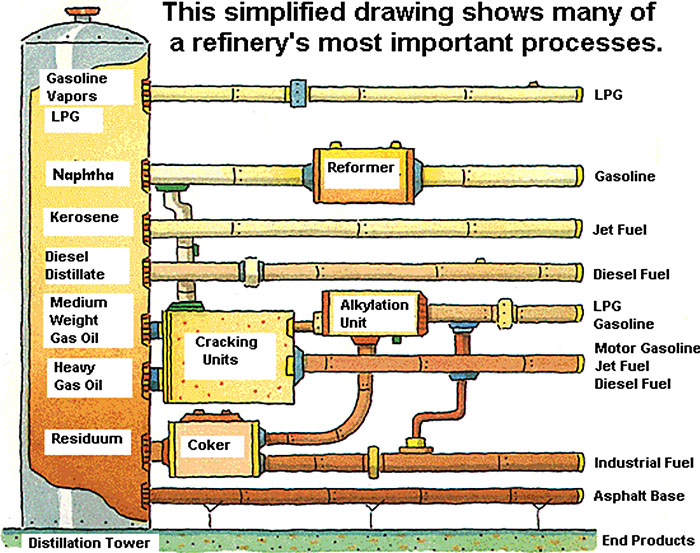
The second and third processes are known as cracking and reforming. Figure 10.8 provides a simplified view of how these processes are used on the various fractions produced through distillation. The heaviest fractions, including the gas oils and residual oils, are lower in value than some of the lighter fractions, so refiners go through a process called “cracking” to break apart the molecules in these fractions. This process can produce some higher-value products from heavier fractions. Cracking is most often utilized to produce gasoline and jet fuel from heavy gas oils. Reforming is typically utilized on lower-value light fractions, again to produce more gasoline. The reforming process involves inducing chemical reactions under pressure to change the composition of the hydrocarbon chain.
The production of final petroleum products differs from refinery to refinery, but in general, the oil refineries in the U.S. are engineered to produce as much gasoline as possible, owing to high demand from the transportation sector. Figure 10.9 shows the composition of output from a typical U.S. refinery.

Nearly half of every barrel of crude oil that goes into a typical U.S. refinery will emerge on the other end as gasoline. Diesel fuel, another transportation fuel, is generally the second-most-produced product from a refinery, representing about one-quarter of each barrel of oil.