
9.4.2a Block Caving
This method, which was developed in the U.S. after WW I, is well suited for mining in weak orebodies. Panels or blocks of ore are undercut. Once undercut, the weak orebody begins to cave under its own weight. The caved ore is drawn off through draw points. As the ore is drawn off, the orebody will continue to cave under its own weight. This process will continue until all of the orebody within the block or panel has been recovered.
Under proper conditions, this underground method can rival economically surface mining! It can do so because it is a bulk or high-volume mining method. But it is not a selective method. In the caving and drawing process, you take everything; and therefore this is not a viable method for following rich mineralized zones, for example. If you were in weak ground, and you wanted to follow mineralized zones, which method would you first consider? Cut and fill? Yes! The method works well for low-grade ores where you have to mine large quantities cheaply to be profitable. Examples include low-grade copper and molybdenum deposits, diamond-bearing Kimberlite pipes, and certain iron ore deposits, among a few others.
Given the foregoing discussion, let’s summarize the conditions that we expect to see for a successful application of block caving.
- Massive orebody (both horizontally and vertically)
- Low grade ore (the method is not selective)
- Orebody must cave easily into manageable pieces
- block - largest cave volume, weakest ores
- panel - intermediate volume, weaker ores
- mass - smaller volume, weak ores
- The host rock, i.e., the hanging wall has to fracture and collapse, following the cave.
- Subsidence of the ground surface above the orebody has to be acceptable.
Note the breakdown of the orebody into the categories of blocks, panels, and masses. These relate to the size of the cave area. If the ore is very, very weak you can have a wide stope. On the other hand, if you try to have a wide stop with a moderately weak ore, you are likely to get bridging within the stope. Caving stops at that point, and it develops into a very dangerous as well as production-killing situation. Thus, the cave volume has to be reduced as the ore becomes marginally stronger. In some mines, they will talk about their panels, and in others, their blocks. Now, you know the reason for this difference in the words they use.
Let’s take a look at a video of block caving before going on. This video will give you a good understanding of the method. There are some other details of note as well:
- Decline and shaft, and the purpose of each
- Ground control measures
- Drawbells
- Undercut level
- Ring drilling
- Materials handling
- LHDs
- Crusher - Orepass
- Conveyor Belt
- Ore skips (hoist)
- Subsidence zone
- Automation
Please watch the following video (3:44) entitled "Block Caving"
Block caving is an underground mining technique used to mine large, massive, low-grade ore bodies such as the deposits at North parks. The ore to be extracted is in the shape of a large irregular block which can be up to 500 meters in height and several hundred meters in length. The development stage at North parks began by gaining access to the ore body with a gently sloping tunnel called the decline and a vertical shaft. The shaft is used to carry mined ore to the surface. The decline is used to transport people and equipment into the mine and to provide fresh air to the mine. The decline and other drives are created by drilling and blasting using a machine called a jumbo. All tunnels are supported by rock bolts and shotcrete to ensure they are safe. After the axis is created, a series of parallel extraction drives are developed from one side of the ore body to the other. Between the extraction drives, draw bells are developed. The undercut level is developed at the same time as the extraction drives. Rings of drill holes are charged and fired from one side of the ore body to the other. The draw bells are drilled and blasted to become a series of funnels that will feed the broken ore to a draw point. This process breaks a layer of rock across the bottom of the block of ore and leaves a large unsupported area which starts fracturing and caving under its own weight. The ore body starts to cave once the undercut is complete and ore is removed from the draw Bell's creating a void. Once the development is complete and the ore body has been undercut, the mining process is relatively simple. With continual fracturing and breaking of the rocks to smaller rocks for extraction without any further blasting. Special low-profile load haul dump vehicles collect the broken off from the draw points and dump it in the underground crusher. The crusher breaks it down into smaller pieces, which are then loaded onto a conveyor. Transported to an ore skip and hoisted, via the vertical shaft, to the surface to be processed to the mill. The block cave ultimately breaks through to the surface and a subsidence zone is formed. Over time, and as more ore is extracted from the cave below, the subsidence zone deepens and widens. One of the innovations at North parks is automated loading which was introduced in 2011. Instead of having miners deep under the ground driving the loaders, they work from the surface controlling the loaders by remote control. Making it safer for the miners.
Here, below, is a view of a block caving operation, which depicts the information that you saw in the video, but in a slightly different form.
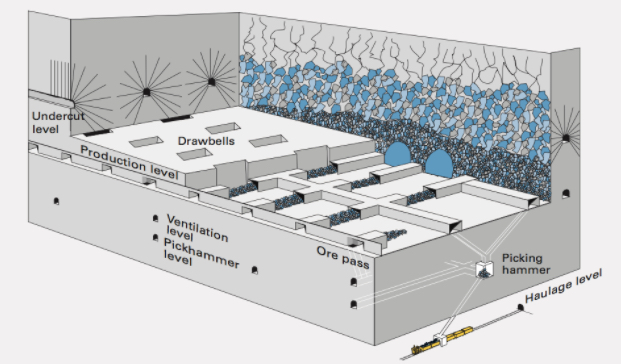
We can summarize what we learned from the video into the following steps for development and exploitation.
Development - Tasks
Development to prepare blocks for production caving is extensive and can take up to several years of advance work. On a per unit cost basis, the development for block caving is no greater than for sublevel caving.
- Sink Shaft and develop decline for access to the orebody from the footwall.
- Drive multiple headings to prepare haulage ways, crosscuts to develop undercut and draw points. Drive other laterals as needed.
- Develop the draw points and ore passes
- Install extensive ground control technologies to stabilize development openings, e.g., shotcrete, cable bolts, steel sets, arches, and so on.
This figure, below, shows these development activities.
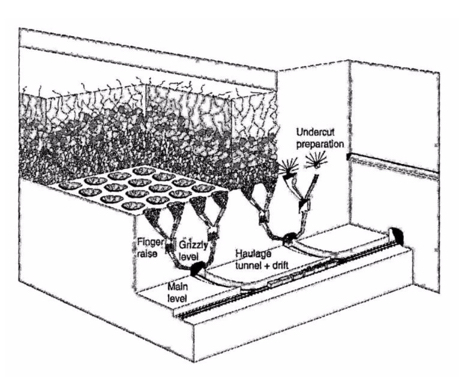
Exploitation - Unit Operations
- Drilling for the undercut using pneumatic- or hydraulic-powered percussion jumbos with a hole size 2 to 3 in.
- Blasting the undercut using ANFO or slurries; and bulk charging by pneumatic loader or pump with electric firing.
- Loading at the draw points with an LHD, or rarely today, a slusher.
- Hauling by LHD from the draw point to an ore pass, and then belt, rail, or truck to a hoist.