
8.3.1: Area Mining
In the left figure, we have relatively constant thicknesses for both overburden and ore. Our first step is to remove the surface vegetation and stockpile the topsoil for later use in reclamation. We will only remove the vegetation and topsoil in the area that we will mine within a period of weeks. Next, we need to gain our initial access to the seam, and we will do this with a box cut. Depending on the hardness and tightness of the overburden, we may need to drill and blast to facilitate its removal. If it is soft enough, we’ll remove it without the need to drill and blast. Depending on the thickness of the overburden, and the required size of the box cut, we will probably use a dragline to make the box cut, although it could be done in certain cases with dozers and scrapers. The overburden from the box cut will be placed to the side of the pit. When the coal seam under the box cut is exposed, we start mining the coal. After the coal in the box cut is removed, a subsequent cut is accomplished and the waste material from the second cut is placed in the space created by the initial box cut. This process continues by making subsequent cuts, putting extracted overburden in the former cut and mining the uncovered coal seam. The collection of sequential cuts forms a strip, and the strips will traverse a portion of the property. Take a look at this figure, and don’t be concerned about the difference between the low wall and the highwall. You can see the box cut. In the lower part of the figure, you can see the strips being mined and the overburden or spoil placed into the adjacent and previously mined strip. The overburden swells in volume when it is extracted, and that’s why you see the piles of spoil protruding above the original contour of the land.

Sometimes, it is difficult to imagine the cuts and strips and how it all progresses. As you look at the pictures and diagrams in this lesson, it will come together for you. Another visual for right now would be to think of a bowling alley with its many bowling lanes. You can think of the bowling alley as the area to be mined, and each lane as a strip. Within each strip, a series of cuts will be made so that the “mining activity” can progress from the beginning to the end of the strip. Mining of the first strip is a little tricky, but once it has been completed then all of the other strips will be completed as shown in the diagram above – remove the overburden, expose the coal seam, mine the coal, cast the overburden from the next cut into the previously mine strip.
Overburden removal in US area mining is commonly accomplished with large draglines, stripping shovels, or in small mines, by conventional excavation and haulage (truck-shovel or dozer-scraper) methods. In some other countries such as Germany, bucket wheel excavators are also used to remove overburden. Dozers and scrapers are also used in clearing vegetation, removing topsoil and subsoil, establishing level benches and surfaces for the dragline, as well as many other activities that involve pushing the spoil. In the next lesson, we’ll look at a video of area mining to recover phosphate, and you will see the prep work done by the dozers as well as the operation of the dragline.
Here is a picture of a Black Thunder Mine. You can see the individual strips where overburden has been placed; and within each strip, note the individual piles. Each pile corresponds to a cut. The uncovered, but unmined coal seam is visible as well. Given the thickness of this seam, on the order of 100’, a large shovel will be used to mine it. If it were thinner, say 10’, then a small shovel could be used, but more likely a wheeled loader. Often, the coal seam is drilled and blasted to facilitate rapid loading of the coal.
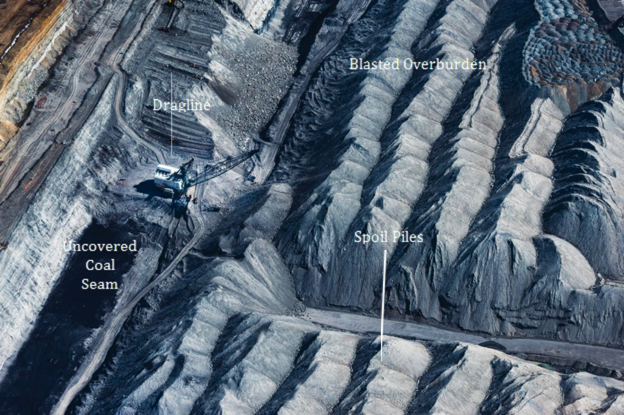
There are a few other elements within this picture that I’d like you to note. Do you see the blasted overburden, and where is the dragline sitting with respect to the top surface of the blasted overburden? Quite a bit lower, right? So, how does this happen?
A dragline has a limited reach, and there is a tradeoff between its reach and the size of the bucket. For example, it may have a reach of 200’ with a 200 yd3 bucket, and 300’ with a 120 yd3 bucket. Without getting into the design details, optimizing the reach and bucket size combination sometimes requires that the overburden be removed in two separate passes. The interesting thing about the process in the Powder River Basin is that they remove up to 40% of the overburden by a process known as cast blasting. In cast blasting, not only does the blast loosen the overburden, but the round is designed such that up to 40% of the overburden is actually thrown or cast into the adjacent strip! They may use a million pounds of ANFO or more to accomplish this!
Dozers are then used to push more of the overburden into the adjacent cut, and importantly, to create a flat and level surface for the dragline to operate. You can also see a temporary haul road developed by the dozers to provide access to the coal seam for haul trucks and to the dragline pad for smaller vehicles to service and supply the dragline.
I want to point out one last detail before leaving this picture. Did you notice the shape of the pile of overburden? They are all very distinct and nearly identical in shape. Do you think that is a coincidence? The piles of material form at an angle known as the angle of repose. This is the angle that a dry, granular, material in a very loose condition will form with respect to the horizontal. The angle of repose is a unique characteristic of the material, whether it is iron ore, coal, #2B crushed stone, flour, or sugar. If we know this angle, we can calculate all sorts of interesting things, such as the maximum angle of a conveyor belt so that the ore will not tumble back on itself or the size of a stock pile.
When it is time to reclaim the strip, bulldozers and scrapers work together to spread these spoil piles. Then the subsoil and top soil are placed back to reclaim and return the land to its original contour lines. Often, the rock layers immediately above the coal seam will be “acid bearing”, i.e., minerals such as pyrites that will create an acidic drainage when ground water percolates through those layers. Acid mine drainage is a great environmental concern, and to reduce the level of acidity under the reclaimed lands, crushed limestone is sometimes added to neutralize acid bearing layers. This process is called liming.
Here is another picture to illustrate the operations of the open cast area mining method.

Draglines
The dragline is an important piece of mining equipment, and you will find it in a variety of, and sometimes unexpected, operations. Let’s look at the fundamental parameters that define draglines for a given application. Each dragline is defined on two parameters: bucket capacity and boom length. Bucket capacity is used to determine the hourly production rate of the equipment, while the dragline’s dumping height and digging depth depend on its boom length. Digging depth, dumping height, and operating radius are the primary parameters that should be considered in selecting appropriate bench dimensions for a particular dragline. These three primary parameters are illustrated in this diagram.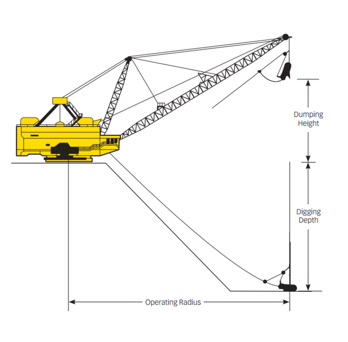
Please take a minute and think about the way that each of these three parameters plays a role in the design and the width of the strips.
Next let’s take a look at the key components of a dragline. You should understand the purpose of the drag, hoist, and dump ropes. You may want to think about the challenges of the structural design of the boom itself, and the tradeoff between bucket capacity and boom length. What about moving the dragline? How does it move about the bench? Very slowly and with great difficulty!!! There are no wheels nor crawler tracks because it is so massive and so heavy that conventional approaches would fail in all but the smallest draglines. Instead, the dragline walks! It sits on a giant cast iron tub so that its enormous weight can be distributed over a large area. On either side of the tub, there is a massive shoe. The shoe is connected to an eccentric cam, and to move, the shoes lift the tub off the bench and propel it forward where it comes to rest. And then, the cycle is repeated. Fortunately, the dragline does not need to move quickly in the course of normal production. However, if you need to move the dragline some distance, say to an adjacent property located on the other side of a highway, it can be a tedious process – like watching grass grow!

Now, let’s look at the operating cycle of the dragline in more detail, with the help of these diagrams.
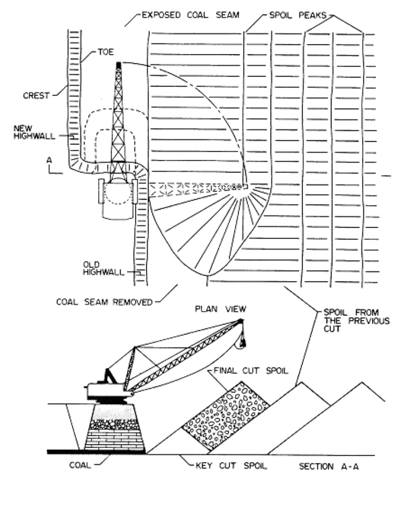
The dragline is positioned on top of the blasted material, which has been leveled and prepared by a dozer. The drag bucket is positioned at its furthest reach, lying on the overburden. The drag rope will begin to pull the bucket towards the tub, and as the drag bucket is pulled, it will dig into the material and the bucket will be filled. Once filled, the dragline operator will begin to hoist the bucket and will begin to swing the boom toward the spoil pile. By the time the bucket reaches the spoil pile, the operator will have completed hoisting the bucket, and will then dump the bucket. Once dumped, the operator will swing back to the position to dig, while at the same time, dropping the drag bucket so that when the swing cycle has been completed, the drag bucket will be lying in position to begin the cycle all over again. A typical time to complete one cycle is 45 seconds.
Bucket Wheel Excavators (BWEs)
Let’s close out this discussion on area mining with a brief mention of bucket wheel excavators (BWE), shown in the picture here. BWEs are massive machines to quickly remove overburden. To gain an appreciation for their size, look for the front-end loader in the lower left part of the picture. Did you find it? These machines have been used successfully in the brown coal fields of Germany for many decades. Some BWEs were imported into the U.S nearly 50 years ago. Unfortunately, the results were disappointing. The characteristics of the overburden were unsuited to the capabilities of BWEs. The bucket wheel excavator is best used for soft and loose overburdens. While these were common in the German lignite fields, they were less common here in the U.S. Consequently, they were never adopted for use in the U.S.